Porosity in Welding: Identifying Common Issues and Implementing Ideal Practices for Avoidance
Porosity in welding is a pervasive problem that commonly goes undetected up until it causes considerable issues with the integrity of welds. In this discussion, we will certainly check out the key aspects contributing to porosity formation, examine its detrimental impacts on weld efficiency, and review the finest techniques that can be taken on to minimize porosity occurrence in welding procedures.
Typical Reasons of Porosity
An additional regular offender behind porosity is the presence of pollutants on the surface of the base steel, such as oil, oil, or rust. When these impurities are not successfully removed prior to welding, they can evaporate and come to be caught in the weld, creating problems. Making use of dirty or wet filler products can introduce impurities right into the weld, adding to porosity problems. To mitigate these common root causes of porosity, thorough cleansing of base metals, proper protecting gas choice, and adherence to optimal welding parameters are crucial practices in attaining top quality, porosity-free welds.
Influence of Porosity on Weld Quality

The presence of porosity in welding can significantly compromise the architectural honesty and mechanical homes of welded joints. Porosity produces voids within the weld steel, damaging its total toughness and load-bearing ability. These spaces work as stress concentration points, making the weld more susceptible to cracking and failure under applied lots. Furthermore, porosity can minimize the weld's resistance to deterioration and other ecological elements, further lessening its longevity and performance.
Welds with high porosity levels tend to show lower influence stamina and reduced capacity to deform plastically prior to fracturing. Porosity can hinder the weld's capacity to successfully transmit pressures, leading to premature weld failure and prospective security dangers in essential structures.
Ideal Practices for Porosity Prevention
To improve the structural stability and high quality of welded joints, what particular actions can be applied to minimize the incident of porosity during the welding procedure? Making use of the proper welding technique for the particular material being welded, such as changing the welding angle and weapon placement, can further stop porosity. Regular examination of welds and instant removal of any issues determined during the welding process are important practices to avoid porosity and produce high-quality welds.
Relevance of Appropriate Welding Techniques
Implementing appropriate welding strategies is critical in making certain the structural stability and top quality of bonded joints, developing upon the structure of effective porosity prevention procedures. Welding strategies straight impact the general toughness and durability of the welded framework. One vital facet of go now appropriate welding techniques is keeping the appropriate warmth input. Excessive heat can result in boosted porosity as a result of the entrapment of gases in the weld swimming pool. Conversely, insufficient warm may cause insufficient combination, developing prospective powerlessness in the joint. Furthermore, making use of the suitable welding criteria, such as voltage, present, and take a trip speed, is critical for achieving audio welds with minimal porosity.
Moreover, the selection of welding process, whether it be MIG, TIG, or stick welding, ought my review here to line up with the specific needs of the job to guarantee optimal outcomes. Proper cleaning try here and preparation of the base steel, along with picking the right filler material, are also vital parts of skillful welding techniques. By adhering to these best practices, welders can reduce the danger of porosity development and generate high-quality, structurally audio welds.
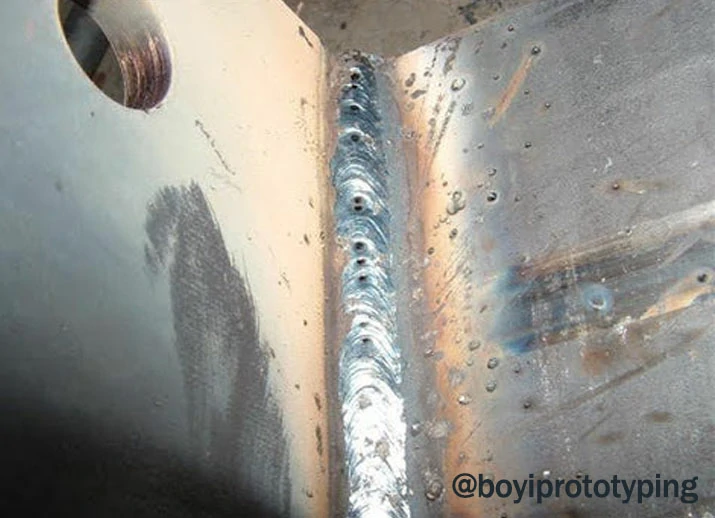
Evaluating and Top Quality Control Procedures
Examining procedures are crucial to detect and prevent porosity in welding, ensuring the toughness and resilience of the last item. Non-destructive testing methods such as ultrasonic testing, radiographic screening, and visual evaluation are typically utilized to determine prospective flaws like porosity.
Post-weld assessments, on the various other hand, assess the last weld for any kind of issues, including porosity, and validate that it fulfills specified standards. Implementing a detailed high quality control plan that consists of extensive testing treatments and assessments is paramount to reducing porosity problems and guaranteeing the overall quality of welded joints.
Verdict
In conclusion, porosity in welding can be a common issue that affects the quality of welds. By determining the common reasons for porosity and applying ideal practices for prevention, such as correct welding techniques and screening steps, welders can make sure premium quality and reputable welds. It is important to prioritize avoidance techniques to reduce the occurrence of porosity and keep the integrity of bonded structures.